Evaluation of Heat Exchanger, Ground Source Heat Pump and Conventional Heating Systems
After two heating seasons, the use of the heat exchanger and ground source heat pump systems resulted to 54 per cent and 45 per cent reduction in energy consumption, report L. Dominguez and Bernardo Predicala in the 2011 Annual Report from the Prairie Swine Centre.Summary
As part of the on-going effort to improve profitability, this study
aims to reduce the energy use in swine barns by evaluating the
performance of various types of heating systems.
A heat exchanger
and a ground source heating system were installed in grow-finish
rooms at Prairie Swine Centre compared with a conventional forced-air
convection heater.
Data from two heating seasons showed that
the use of heat exchanger and ground source heat pump led to
54 per cent and 45 per cent reduction in energy consumption for heating and
ventilation, respectively, compared to the conventional heater.
Introduction
Energy cost is one component of production cost that can be further
reduced by using energy more efficiently or reducing overall energy
consumption. Results from previous work showed that space
heating is an area where energy reduction can be achieved (PSC
Annual Report 2008, p19-20).
This study aimed to evaluate the
performance of a heat recovery ventilator (HRV or heat exchanger),
a ground source heat pump (GSHP) and a conventional heating
system in grow-finish rooms in terms of energy consumption,
in-barn environment, and animal productivity. To achieve a
detailed comparison of the various heating systems, the study was
conducted over several seasons.
Materials and Methods
To compare their performance, the three heating systems were
installed separately in 120-head grow-finish rooms at the Prairie Swine Centre. The
rooms had similar building construction, pen configuration and
pig capacity.
For each grow-finish cycle, a total of 360 pigs were
distributed equally to the three rooms. Metering equipment were
installed to monitor the electricity consumption of the heat pump,
heaters, lights, ventilation and recirculation fans, as well as the natural gas consumption of the forced-convection heaters in the
heat exchanger and control rooms.
The HRV system was a 1500-cfm aluminum core heat recovery
ventilator (Figure 1). The heat exchanger recovers the heat energy
from exhaust air stream by heat transfer to the incoming fresh air
stream.
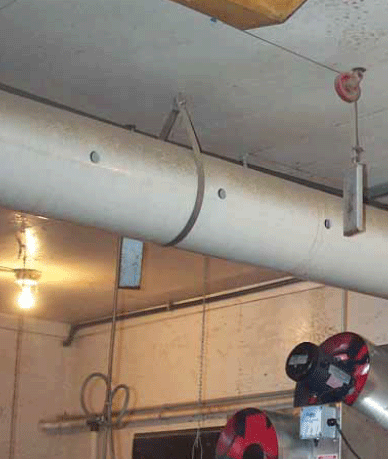
Figure 2 displays the components of the GSHP system, alternatively known as geothermal heat pump, geo-exchange, earth-coupled or earth-energy system, used in the study. It is composed of a heat pump and 1800ft of 3/4” diameter polyethylene pipes buried in 8.5 to 10.0-ft deep trenches on the ground beside the barn. The buried pipes contained 20 per cent methanol and 80 per cent water solution for absorbing heat from the ground for heating and for using the ground as heat sink when cooling is needed.
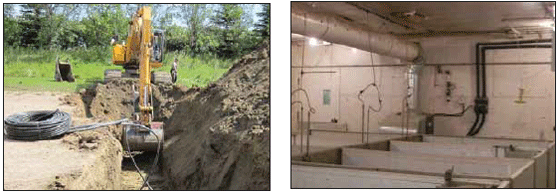
Results and Discussions
Three grow-finish cycles were completed to evaluate the impact of
the various types of heating systems in swine rooms. The first grow-
finish cycle was conducted from October to December 2010 and the
mild weather condition during the trial did not require the use of
heating, thus no data for this cycle is presented.
Data collection for
the second and third cycles were conducted from January to March
2011 and from December 2011 to February 2012, respectively. For
clarity, the January to March 2011 data collection is referred to as
Trial 1 and the December 2011 to February 2012 data collection is
Trial 2.
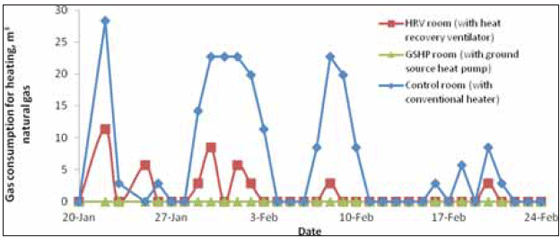
Daily gas consumption for heating each of
the three rooms for the two trials are shown
in Figures 3 and 4, respectively. For the
duration of the Trial 1, the conventional forced
convection heater (control) room consumed
a total of 226.71 cubic metres of natural gas while the
HRV room consumed 42.51 cubic metres of natural gas
for heating. The GSHP room did not use any
natural gas but it consumed a total of 1,206kWh of electricity (mainly to run the heat
pump) to heat the room.
For Trial 2, the control room consumed a total of 224.0 cubic metres of natural
gas while the HRV room consumed 31.2 cubic metres of natural gas for
heating. The GSHP room consumed 714kWh of electricity to heat
the room.
To compare the systems better, all energy consumption data were
converted to gigajoules (GJ). Energy consumption for heating
and ventilation of each of the three rooms for Trials 1 and 2 are
presented in Figures 5 and 6. The energy consumption for heating
included both the electrical and heating fuel consumption of the
heat pump and heaters while that for ventilation included the
electrical consumption for both ventilation
and recirculation fans.
Data for both trials showed that among the
three heating systems, the heat exchanger
required the least energy for heating but
had the highest consumption for ventilation.
The heating requirement was reduced as the
heat exchanger pre-heated the incoming
cold air with heat from the warm exhaust
air. In terms of function, the heat exchanger
basically replaced the stage 1 fan and
because its power rating was higher than that of a regular stage 1 fan, the energy requirement to ventilate
the HRV room was higher than the conventional room.
Nevertheless, the use of heat exchanger led to 52 per cent less total energy
used for heating and ventilation in Trial 1 and 57 per cent less in Trial 2
than the conventional room with forced-convection heater.
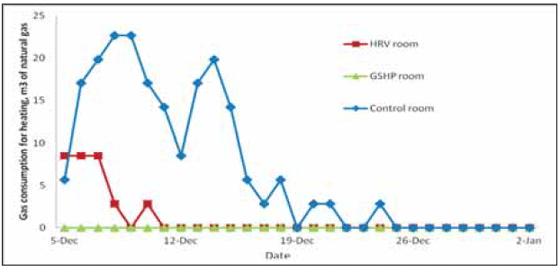
The GSHP required less energy to extract heat from the ground and
to heat the room air compared to the conventional heater. The use
of the GSHP system led to 39 per cent reduction in total energy needed
for heating and ventilation for Trial 1 and 52 per cent reduction in Trial 2
compared to the control room.
When combined over the two heating trials, the HRV room and
GSHP room used 54 per cent and 45 per cent less total energy for heating and
ventilation, respectively, than the conventional room.
The performance of the pigs in terms of average
daily gain, feed intake and feed efficiency were
quite similar as shown in Table 1. However, the feed
intake and feed efficiency values in the rooms with
GSHP and heat exchanger are lower than that of the
conventional heater room.
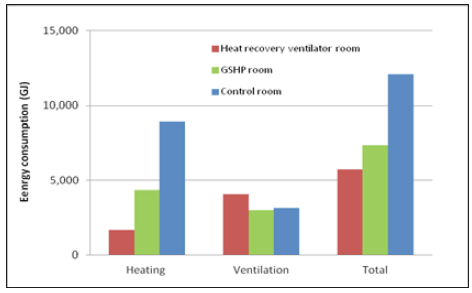
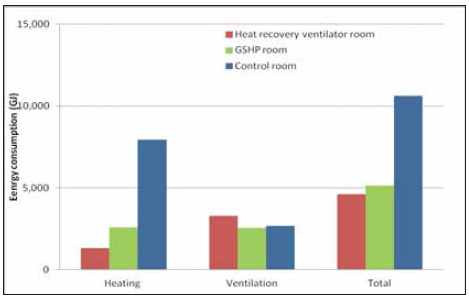
Table 1. Average daily gain (kg/day), feed intake (kg/day and pig) and feed ffficiency in the three rooms for the two heating trials | ||||
---|---|---|---|---|
Room | ADG (kg/day) | ADFI (kg/day-pig) | Feed Efficiency | |
Trial 1 | Control | 0.99 | 2.55 | 2.58 |
HRV | 0.97 | 2.37 | 2.44 | |
GSHP | 0.99 | 2.48 | 2.51 | |
Trial 2 | Control | 0.98 | 2.52 | 2.57 |
HRV | 0.97 | 2.44 | 2.52 | |
GSHP | 0.98 | 2.42 | 2.47 |
Conclusions
After two heating seasons, the use of the heat
exchanger and ground source heat pump systems
resulted to 54 per cent and 45 per cent reduction, respectively,
in energy consumption for heating and ventilation
relative to the conventional forced-convection
heater.
Pigs in the three rooms performed similarly
in terms of average daily gain. Pigs in the heat exchanger and
ground source heat pump rooms, however, have
slightly lower feed intake and more favourable feed
efficiency than those in the forced-convection heater
room.
Additional trials during the summer months
are being conducted to assess the cooling effect of
the GSHP system and its impact on overall energy
use and pig performance.
Acknowledgement
Project funding provided by Advancing Canadian
Agriculture and Agri-Food Saskatchewan and
Saskatchewan Agriculture Development Fund.
Strategic funding provided by Sask Pork, Alberta
Pork, Manitoba Pork Council and Saskatchewan
Agriculture and Food Development Fund.
October 2012