Waste Not, Want Not: Anaerobic Digestion
Farm Case Study No. 32 from BPEX describes the anaerobic digestion (AD) system at the farm of James Hart and Jeremy Iles in Gloucestershire, UK.Farm Facts
Name: James Hart and Jeremy Iles
Location: Gloucestershire
Farm size and enterprise: 400 sows, farrow-to-finish,
Four broiler sheds (150,000 birds), 600 hectares of arable and
100 suckler cows
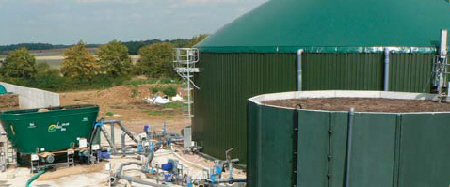
Background
James Hart and Jeremy Iles had seen the increased interest in
anaerobic digestion and with their combination of
available pig slurry, farmyard manure (FYM), poultry litter and arable land
decided they had the sufficient facilities and raw materials
to resource an anaerobic plant. The farm also has the
capacity to use the generated heat and electricity on site.
The project was partly funded (40 per cent) by a Rural
Development Programme for England (RDPE) grant.
This extra funding means that they are not eligible to
claim the Feed-in Tariff payments, however, they receive
Renewable Obligation Certificate (ROC) payments for
generated electricity.
Keeping the system as simple as possible and not relying
on imported food wastes has helped towards the success
of the plant.
Benefits
- The AD is utilising farm resources and adding value
- Guaranteed ROC payments for energy produced until 2027
- The business is protected against future gas and electricity price rises
- It improves the farm’s environmental credentials
- Projected good return on capital invested.
* "We seized on a solution to realise extra value from our waste product, while creating a further income stream from both farm businesses." |
James Hart, owner
|
The System
- The continuous flow, mesosphilic AD plant cost £1.2 million to install with the help of a £440,000 RDPE grant
- The plant was designed and project managed by the partners. Building work took eight months and the plant was on-line in March 2011
- A prototype AD plant was built to help understand the technology and gas yield that could be produced
- Feedstocks include pig slurry, FYM, chicken litter and maize silage
- The gas produced is used to power a combined heat and power (CHP) unit which produces electricity and heat
- The heat is used in the farmhouse and there is also the potential to heat the pig buildings and local school
- Surplus electricity is exported to the grid
- Digestate is used on their arable land.
Key to Success
- Do your research first, set up a prototype AD unit if possible
- Choose the right renewable energy for your site
- Choose a recommended and reputable supplier
- Keep your system as simple as possible and where feasible do not rely on imported food waste, unless you have a long term contract
- It is a 'busy business', needing constant attention 24 hours a day, even when running well.
August 2012