Danish Pig Research Centre: Annual Report 2010: Environmental Technology
The 2010 annual report from the Danish Pig Research Centre outlines the latest research on pig house environmental management.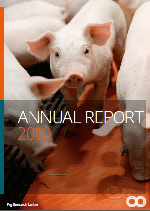
Testing of environmental technology
Pig Research Centre (PRC) participates in
the development and testing of environmental
technologies used by pig producers
to limit ammonia and odour emissions.
The aim is to ensure that these technologies
are efficient in terms of their environmental
impact as well as the economy in
using them.
A ‘technology list’ made by the Danish
Environmental Protection Agency
outlines the systems that have already
been tested sufficiently (see the table),
while PRC is continuously testing new
products and technologies. A wide range
of methods is available for reduction
of ammonia emissions from pig houses
whereas only few reduce odour emissions.
Below, current investigations of new or
improved environmental technologies are
described.
Dorset air cleaner
Rotor A/S, a Danish ventilation company,
markets a biological air cleaner from the
Dutch company Dorset. The air cleaner
is approved for use in the Netherlands
and Germany, but foreign trials revealed
that the consumption of water and the
production of discharge water were too
high for the air cleaner to be used on pig
farms in Denmark.
The air cleaner was therefore modified
and in 2009 set up on a Danish finisher
farm where PRC tested its efficiency in
reducing ammonia and odour over a year.
Data shows that both the consumption
as well as the discharge of water were
successfully reduced. The air cleaner
also reduces emissions of both ammonia
and odour under Danish production
conditions. The results of the trial will be
published in the autumn 2010.
Three-step air cleaner from SKOV A/S
For years, Danish pig producers have been using the Farm AirClean BIO system, a biological air cleaning system from SKOV A/S. Through trials, PRC has demonstrated that odour concentrations dropped by 30 per cent in the summer and by 50 per cent in the winter when ventilation air from pig houses was cleaned. Ammonia concentrations of 4-9 ppm were reduced to 1-2 ppm.
Technology list of the Danish Environmental Protection Agency of approved environmental technologies and their efficiency in reducing ammonia and odour emissions from pig houses. | ||
Technology | NH3 | Odour |
---|---|---|
Feeding | ||
Feeding efficiency | 10-20% | 0 |
Reduced protein | 15% if 10% less crude protein | 0 |
Benzoic acid | 1% per g/feed unit | 0 |
Slurry technologies | ||
Cooling of slurry | 30% | 0 |
Acidification of slurry | 70% | 0 |
Air cleaning | ||
Air cleaning with acid | 90% | 0 |
Biological air cleaning | 70% | 0 |
SKOV A/S has improved the system to
increase the reduction in odour. The
controller was optimised and the washing
robot in the air cleaner modified. Furthermore,
a third filter element was installed,
ie. the air cleaner may consist of three vertical
cellulose filters if large odour reductions
are required. To ensure that all filters are evenly loaded with air, a perforated air
distribution board is fitted before the first
filter element.
Recordings made in Germany in 2009
indicate that the air cleaner is improved
in terms of odour reduction. PRC is now
investigating the air cleaner to document
the reduction in ammonia and odour and
the costs of running the system on a Danish
finisher farm.
Air cleaner from Munters A/S

In the summer 2009, PRC made a series of preliminary recordings of an air cleaning system developed by Munters A/S (previously Turbovent) that demonstrated a 90 per cent reduction in ammonia. The system
was subsequently modified by Munters
A/S, and is now ready for a comprehensive
test. The aim is to document its efficiency
in reducing ammonia emissions over a
long period of time and the costs of running
the system.
The air cleaner is constructed as a tube
without filter elements. Nozzles at the
bottom of the air cleaner sprinkle acidic
water into the air stream whereby air is
cleaned. A drip catch at the top of the
system retains the acidic water in the air
cleaner.
It remains to be clarified if acidic water is
released with the exhaust air from such
systems to potentially damage building
parts. Part of the investigation of Munters’
system thus concerns the amount of
acidic water released from air cleaner to
the surrounding environment.
Cooling of inlet air
Odour emissions from pig houses are highest
in the summer when ventilation systems
run on maximum performance. In an
investigation of a ground cooling/heating
system from the Dutch company INNO+,
it was therefore determined whether
ammonia and odour emissions could be
reduced when the inlet air in a farrowing
house was warmed or cooled, respectively,
so that the ventilation rates in the housing
unit varied less. Over a year, the system
was capable of keeping the temperature
of the inlet air to the farrowing house
between 4.3 and 19.6 C° despite the fact
the outdoor temperatures ranged from -4
to +32 C°.
Odour emissions from the trial facility
generally tended to be lower in the summer.
However, on the hottest summer
days, odour emissions from the trial facility
were 39 per cent lower than from the control
facility, which shows that cooling the inlet
air may neutralize the release of very high
odour emissions in warm weather. It was not possible to record a significantly lower
ammonia emission over an entire year.
Pit ventilation
Ammonia and odour originate from slurry, and PRC investigated if the majority of these substances can be collected in air that is emitted through pit ventilation. If so, a large reduction in ammonia and odour emissions from pig houses will be possible by cleaning this air with an efficient air cleaner.

It was studied how much odour and ammonia
emission originates from pit ventilation
and ceiling exhaust, respectively, at a
pit ventilation capacity of 16 and 54 m3/h
per pig place, respectively. The remaining
ventilation air up to maximum output
(100 m3/h) was emitted through the
ceiling.
The results demonstrated that when 16
m3/h were sucked out through pit ventilation,
61 per cent of the overall odour emissions
and 70 per cent of ammonia emissions from the
pig house originated from the pit ventilation.
When 54 m3/h were sucked out trough
pit ventilation, 90 per cent of odour emissions
and 94 per cent of ammonia emissions were
collected in the pit ventilation. Here the
overall emissions of both odour and ammonia
from the pig house were significantly
higher than during pit ventilation at
16 m3/h, and higher than expected. The
most realistic way forward is therefore
setting pit ventilation at approx. 10-20 per cent
of maximum capacity.
The working environment in the pig
house was equally good with both settings
evaluated on the basis of ammonia
and odour concentrations in the room.
Frequent emptying of slurry pits
In 2009, PRC investigated whether it is
possible to reduce odour emissions from
pig houses with slurry systems by changing
the frequency of emptying of the pits.
In a trial section, slurry was emptied once a week, whereas it was emptied in the
control section when the pits were full (40
cm). In the period June-November, 50 per cent
lower odour emissions were recorded the
day after the trial section was emptied
compared with the control section. However,
there was no significant difference
in ammonia emission from the section
regardless of emptying strategy.
The investigation is currently being
repeated in the climate chambers at PRC’s
Experimental Station Grønhøj where it is
being studied for how long the reduced
odour emissions last after emptying.
Acidification
Infarm A/S is the only company with a
Technology Sheet on acidification of slurry
with 65-70 per cent reduction in ammonia emission
from pig houses.
In the summer 2010, the company Jørgen
Hyldgård Staldservice A/S installed its first
acidification system on a finisher farm
where PRC will test the system.
Further Reading
![]() |
- | Go to our previous article on this report by clicking here. |
September 2011